Purpose
The RT9750 is a 6A smart load switch battery charger, which integrates an internal load switch with charge pump control and 3-path constant current/constant voltage regulation, a 5-way hardware protection, and a 8-Channel 12-bit analog-to-digital converter. This document explains the function and use of the RT9750 evaluation board (EVB), and provides information to enable operation, modification of the evaluation board and circuit to suit individual requirements.
Introduction
General Product Information
The RT9750 is a 6A smart load switch battery charger, which integrates an internal load switch with charge pump control and 3-path constant current/constant voltage regulation, a 5-way hardware protection, and a 8-Channel 12-bit analog-to-digital converter. The RT9750 provides the accurate analog-to-digital converter for voltage/current measurement by I2C serial interface to report the battery charging parameters and 3-way software protection and flags.
Product Feature
- Internal Load Switch with Charge Pump Control
►Dual NFETs in a Back to Back Configuration
►Internal Charge Pump Control
- 3-Path CC/CV Regulation
►Input Current Regulation (ICR)
►Output Voltage Regulation (OVR)
►Battery Voltage Regulation (BVR)
- 5-Way Hardware Protection
►VBUS Over-Voltage Protection (VBUS_OVP)
►Drop-Out Over-Voltage Protection (VDR_OVP)
►Reverse Over-Current Protection (RE_OCP)
►Junction Over-Temperature Protection (TJ_OTP)
►Input Over-Current Protection (IOC_OCP)
- 8-Channel 12-bit ADC
►High Accuracy of 12-bit Resolution
►8-Channel for Voltage/Current Measurement
►High Speed Data Rate for 8/16 Times Average per Channel
- 3-Way Software Protection
►Drop-Out Over-Voltage Protection Alarm (VDR_ALM)
►TS of the VBUS Over-Temperature Protection (TBUS_OTP)
►TS of the BAT Over-Temperature Protection (TBAT_OTP)
Key Performance Summary Table
Key Features
|
Evaluation Board Number : PCB095_V1
|
Input Voltage
|
3V to 6V
|
Output Voltage
|
3V to 6V
|
Maximum Output Current
|
6A
|
Marking & Package Type
|
RT9750WSC, WL-CSP-42B 2.75x3.05
|
Bench Test Setup Conditions
Headers Description and Placement
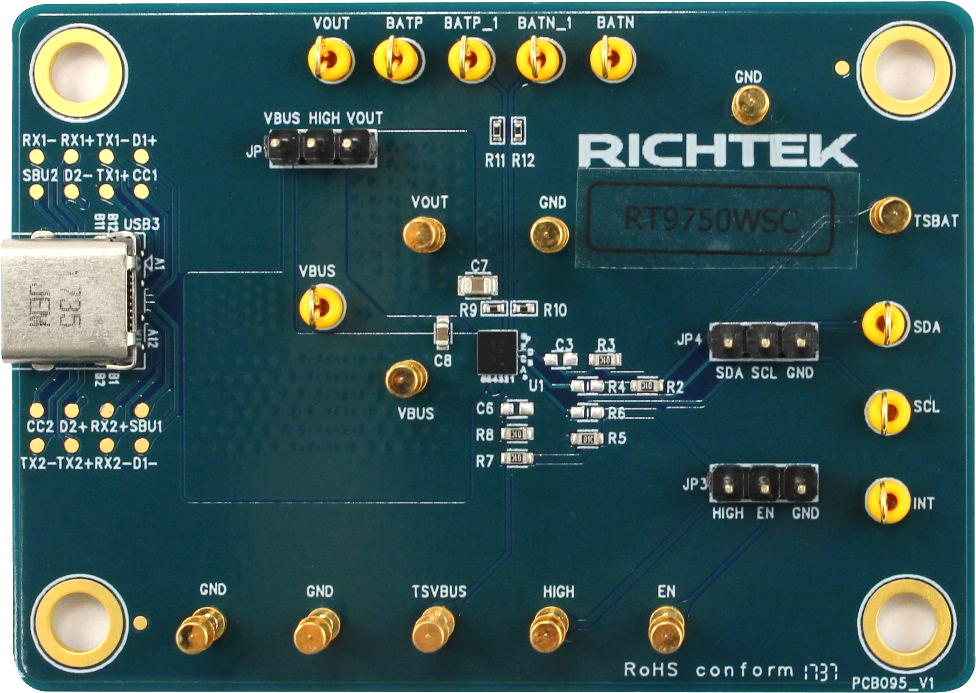
Carefully inspect all the components used in the EVB according to the following Bill of Materials table, and then make sure all the components are undamaged and correctly installed. If there is any missing or damaged component, which may occur during transportation, please contact our distributors or e-mail us at evb_service@richtek.com.
Test Points
The EVB is provided with the test points and pin names listed in the table below.
Test point/
Pin name
|
Signal
|
Comment (expected waveforms or voltage levels on test points)
|
VBUS
|
Input voltage
|
DC input power supply.
|
VOUT
|
Output voltage
|
Battery connection point to positive terminal of the battery pack.
|
GND
|
Ground
|
Ground.
|
TSVBUS
|
VBUS temperature qualification voltage input
|
VBUS temperature qualification voltage input. Require an external resistor divider and a voltage reference.
|
TSBAT
|
VBAT temperature qualification voltage input
|
Battery temperature qualification voltage input. Require an external resistor divider and a voltage reference.
|
EN
|
Enable pin
|
Device enable control pin. Pull low to disable device. I2C not available
when disabled.
|
INT
|
Intterrupt
|
Open drain interrupt output. connect to pull-up voltage via 10kΩ pull-up resistor. Normally high, the INT pin sends an active low.
|
SDA
|
SDA
|
I2C interface data. Connect to pull-up voltage via 10kΩ pull-up resistor.
|
SCL
|
SCL
|
I2C interface clock. Connect to pull-up voltage via 10kΩ pull-up resistor.
|
Power-up & Measurement Procedure
1. Connect input power (3V < VBUS < 6V) and input ground to VIN and GND test pins respectively.
2. Connect positive end and negative terminals of VBAT to VOUT and GND test pins respectively.
3. There is a 3-pin header “High” for pull-up control. To use a jumper at “VBUS” option to tie pull up pin to input power VIN. Use a jumper at “VOUT” option to tie pull-up test pin to battery.
4. There is a 3-pin header “EN” for enable control. To use a jumper at “High” option to tie EN test pin to high level for enabling the device. Inversely, to use a jumper at “GND” option to tie EN test pin and ground GND for disabling the device.
Schematic, Bill of Materials & Board Layout
EVB Schematic Diagram
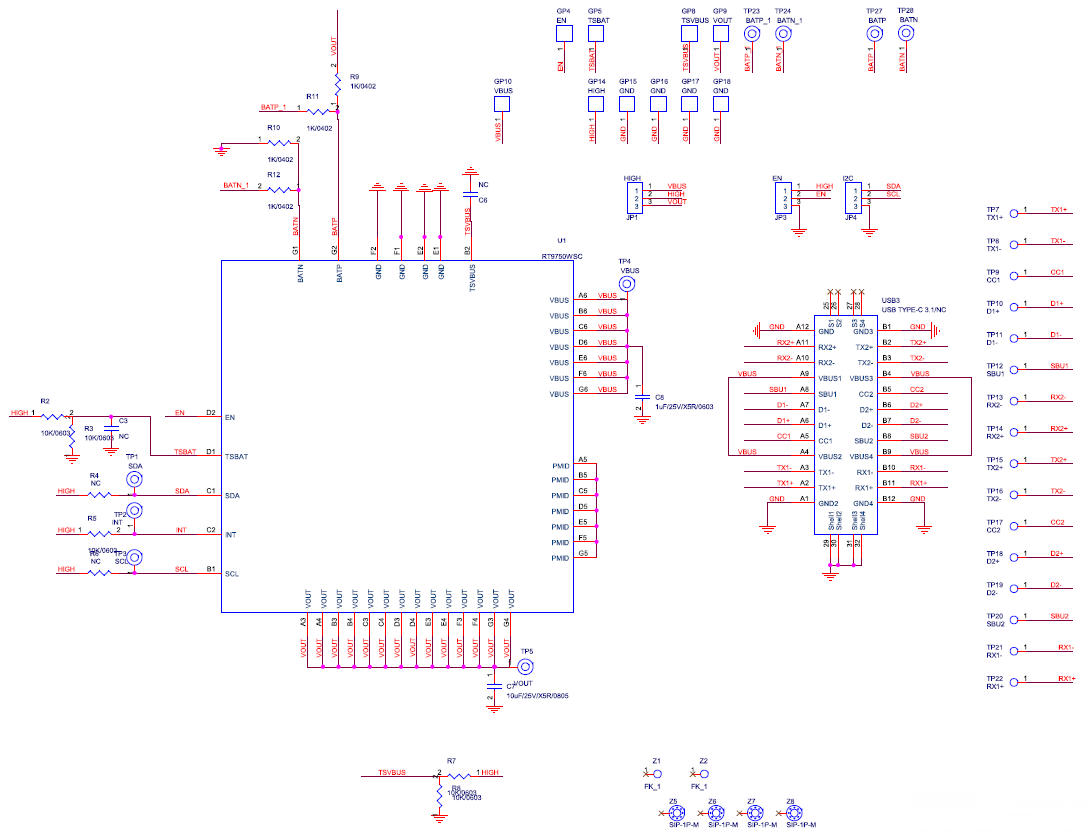
Bill of Materials
Reference
|
Qty
|
Part Number
|
Description
|
Package
|
Manufacturer
|
U1
|
1
|
RT9750WSC
|
Smart Load Switch
|
WL-CSP-42B 2.75x3.05
|
RICHTEK
|
C7
|
1
|
GRM21BR61E106KA73L
|
10µF/25V/X5R
|
C-0805
|
muRata
|
C8
|
1
|
C1608X5R1E105K080AC
|
1µF/25V/X5R
|
C-0603
|
TDK
|
R2, R3, R5, R7, R8
|
5
|
WR06X1002FTL
|
10k
|
R-0603
|
WALSIN
|
R9, R10, R11, R12
|
4
|
WR04X1001FTL
|
1k/1%
|
R-0402
|
WALSIN
|
PCB Layout
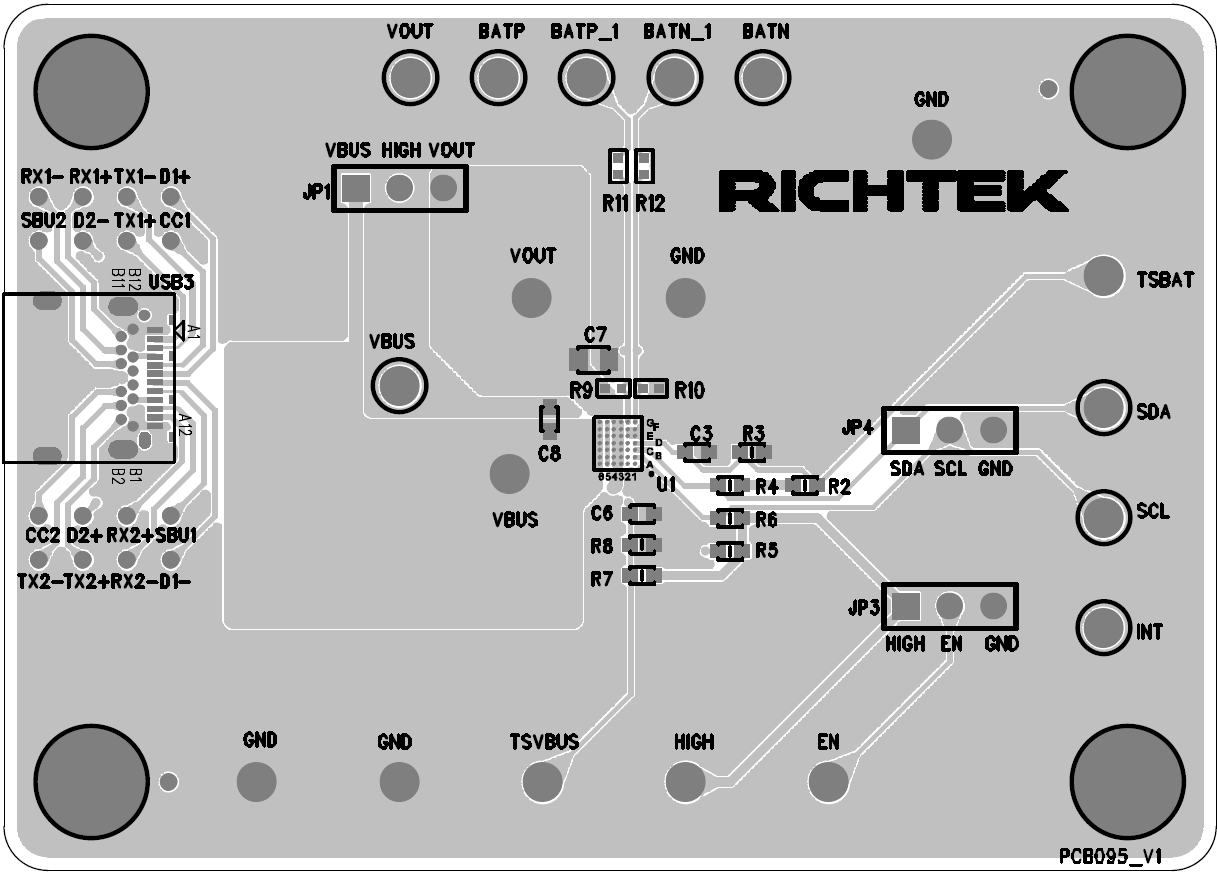
Top View (1st layer)
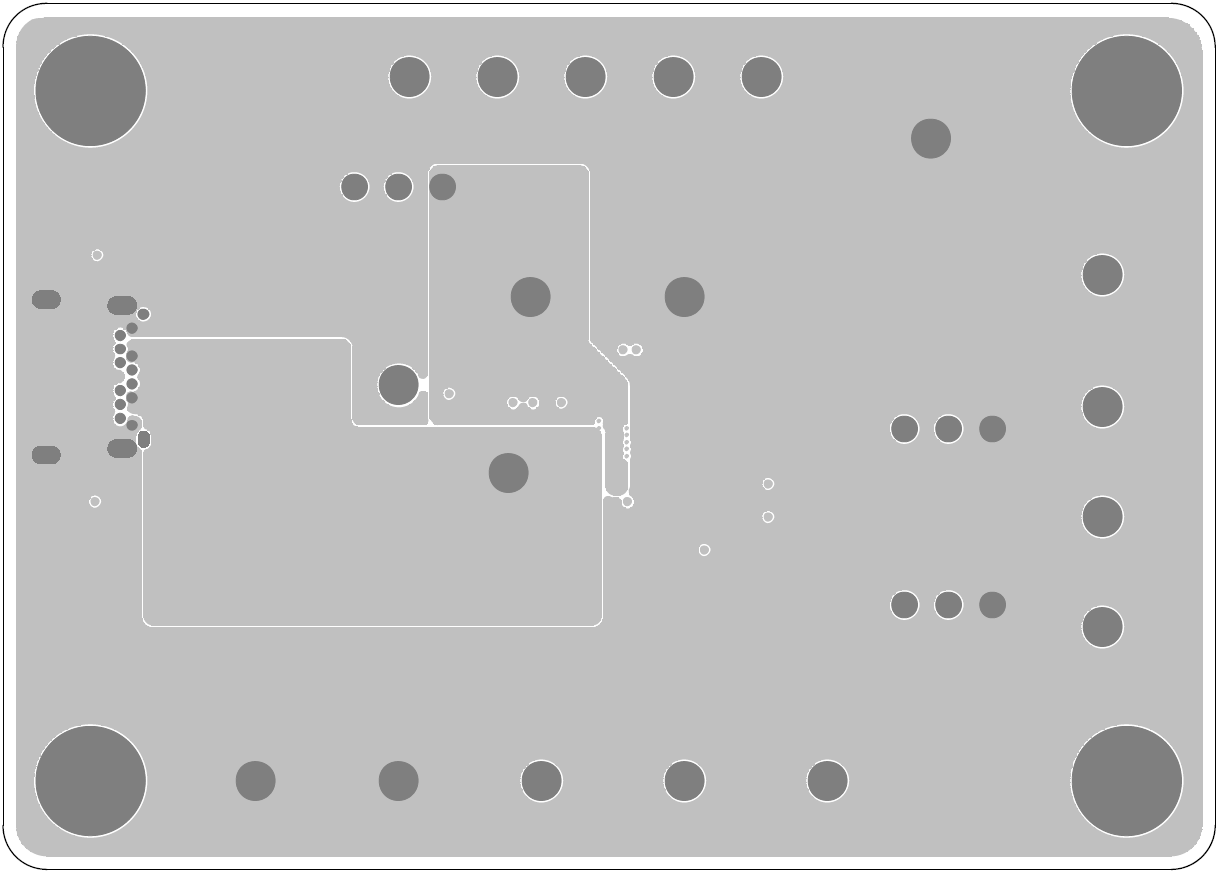
PCB Layout—Inner Side (2nd Layer)
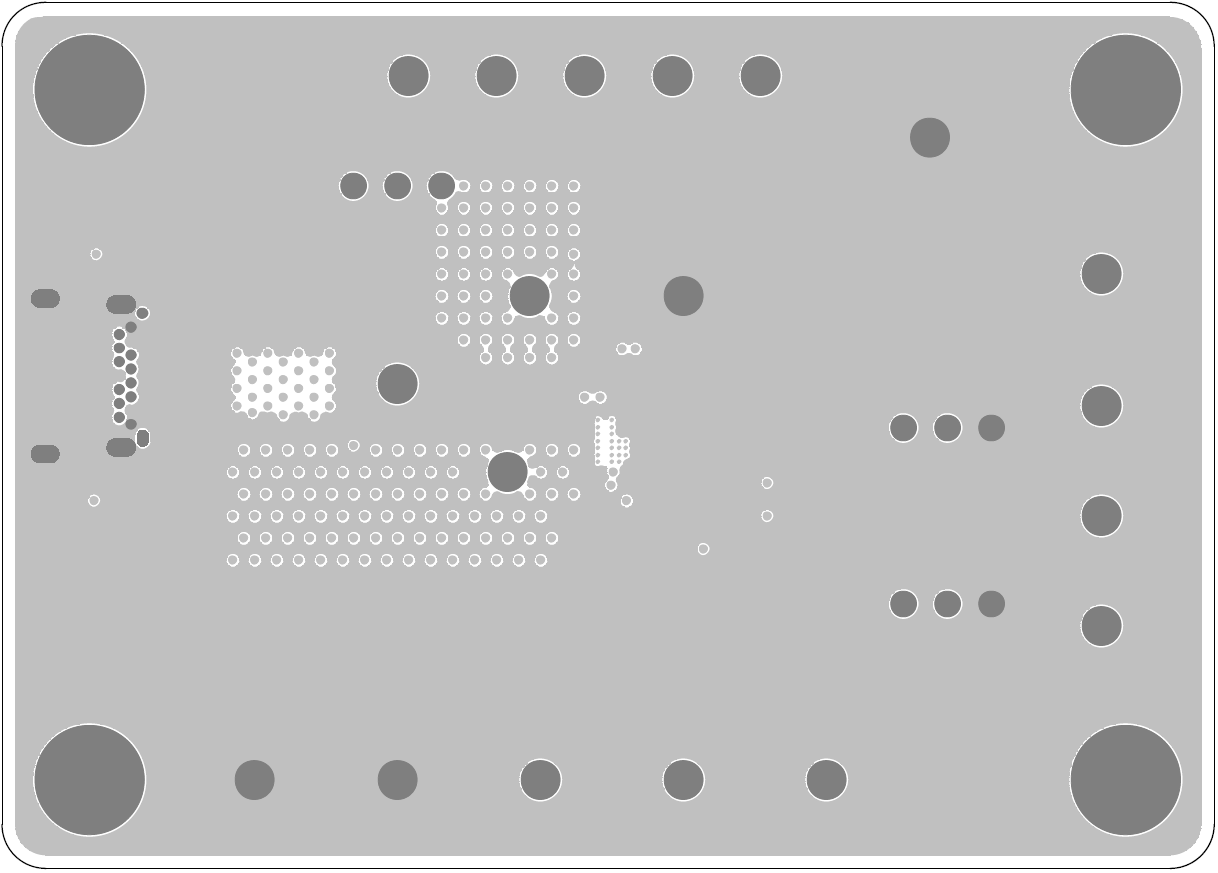
PCB Layout—Inner Side (3rd Layer)
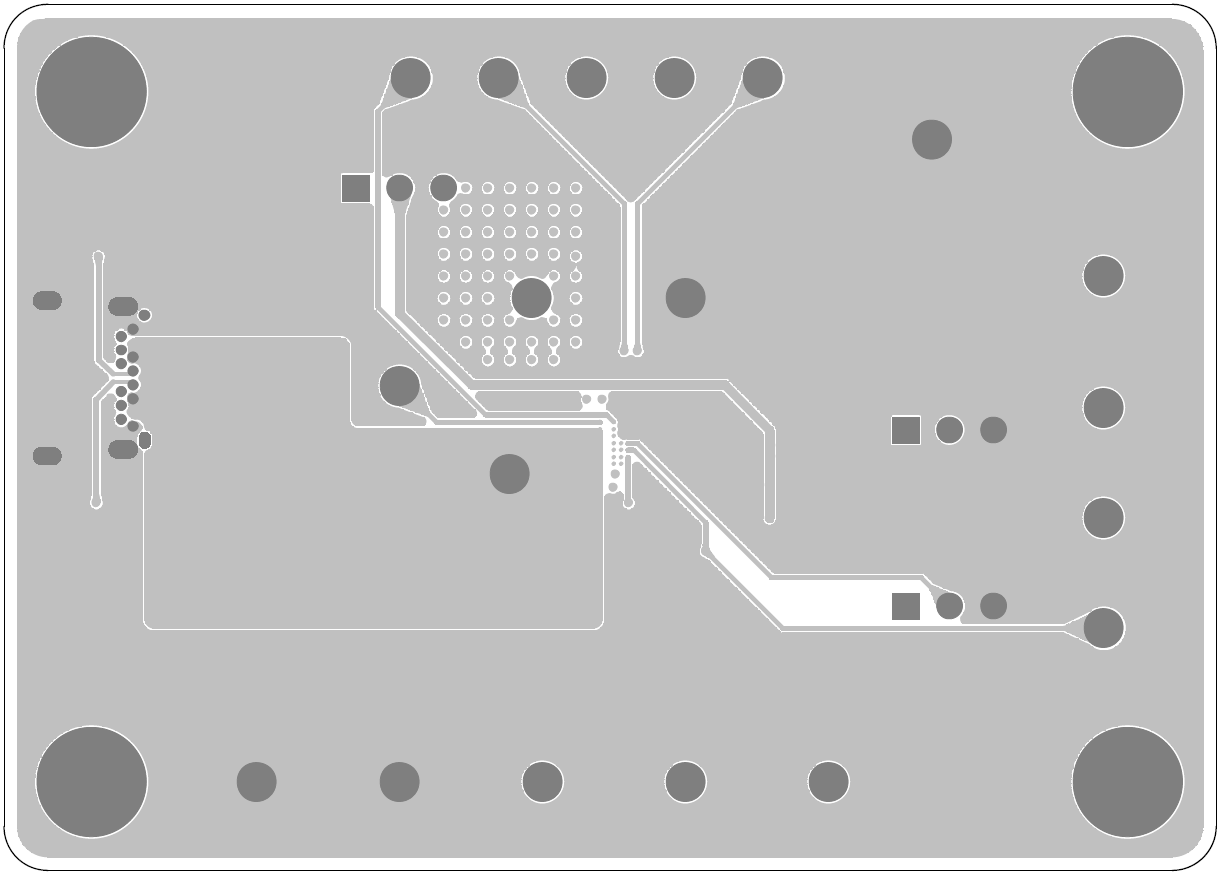
Bottom View (4th Layer)